9 Steps to Stick Weld Cast Iron: And How to Avoid Preheating
Stick welding (SMAW) cast iron is the most economical, versatile, and popular way for the job. Stick welding is ideal for a quick repair job and has many welding rods for cast iron, and in some cases, you can weld castings without preheating.
Weldpundit already has a general article on cast iron welding if you are completely unfamiliar with the topic.
Table of Contents
- 1. Identify the cast iron alloy
- 2. Gather the equipment you need
- 3. Clean the surface
- 4. Prepare the casting
- 5. Preheat the casting to avoid temperature differences
- 6. Weld short beads to prevent uneven temperatures
- 7. Peen each bead to prevent shrinkage stress
- 8. Reheat the casting to fix temperature differences
- 9. Protect the casting so it can cool down slowly
- Stick weld cast iron without preheating
First, let’s see how to stick weld cast iron with preheating in 9 steps.
1. Identify the cast iron alloy
Almost certainly, you have gray cast iron, since it’s by far the most common type. But you might have nodular or malleable iron. These two have some degree of ductility (how much they can bend without breaking).
Weldpundit already has an article about how to identify metals, but here are the basics to figure out the casting you have.
A spark test is an excellent method to identify metals, but you must have identified sample metals to compare them with your workpiece. In a nutshell, gray iron has short and reddish sparks, but ductile irons have longer and yellowish sparks, closer to steel sparks.
If you have a broken part, gray iron has a characteristic dark-gray color. Malleable cast iron has a white, steely surface but gets gray towards the center. Nodular iron’s color is more similar to gray iron.
You can distinguish gray iron from the two ductile irons by testing their hardness:
- You can use a center punch and a hammer on them. If the crater that is left has a smooth surface, it’s gray iron. If the crater has a burr, it’s a malleable or nodular iron.
- You can also try to drill the casting. If the chips are like powder, it’s gray iron. If they are somewhat continuous, it’s ductile iron.
- If the chips are long and very ductile, you might have cast steel rather than cast iron.
If you cannot drill the casting, it’s hardened by the manufacturer or by former welding. If so, it’s too hard to weld it with success. However, if it’s localized, then you can remove the affected area before proceeding.
Since gray iron is the most popular, the rest of the guide will be about it. Now, let’s see what equipment you need.
2. Gather the equipment you need
You need to gather all the necessary welding personal protective equipment:
- Welding helmet.
- Safety glasses.
- Face shield.
- Earplugs or earmuffs.
- Thick welding gloves.
- Fire-resistant clothes that cover all of your body.
- Leather boots.
- Welding respirator.
Gather all the welding tools for the job:
- Equipment to clean and prepare the casting:
- Angle grinder with a grinding or flap disc or a
- Die grinder with a carbide burr or
- Chisel and hammer.
- A steel wire brush.
- The preheating equipment, either an oven or a flame torch.
- Temperature sticks or an infrared (IR) digital thermometer to check the casting’s temperature.
- A drill if you want to repair a crack.
- A small ball-peen hammer to peen each bead you make.
- The equipment you will use to cool down the casting after welding, for example, fiberglass material or dry sand.
What welding rod do you need?
The best overall welding rod for cast iron is the ENiFe-CI (or ENi55). It can weld dirty castings, cast iron to steel, and the weld metal is most often machinable.
After that, you can use an ENi-CI (or ENi99) that is very machinable but expensive.
Finally, you can choose an ESt rod that is cheap and great for small repairs, but it’s not machinable.
Welding cast iron with typical welding rods is not recommended because the weld metal will absorb carbon and become brittle. As a result, it will crack as it cools down.
If you cannot obtain a cast-iron rod and you cannot postpone welding, your best bet for a quick fix is the E7018 rod. That’s because it has the highest ductility and leaves the thickest slag covering. But you will need a much higher preheating temperature, perfect peening, and a very slow cool down to prevent cracking.
The rutile E6013 and even more the cellulosic E6011 rod have the highest chances of failure.
Select a rod size that will fill the groove with a single pass bead to avoid putting too much heat in the casting. The common rod sizes are 3/32″ (2.4 mm) and 1/8″ (3.2 mm).
If you want to avoid the high cost of nickel rods, try at least to obtain one or two. First, use them for welding the surface of the joint. We call this buttering. This method seals the cast iron so no carbon or impurities can pass beyond the new nickel surface. After that, you can use other cheaper rods, such as the ESt or even the E7018, to fill the joint.
Weldpundit already has a detailed article on cast-iron welding rods.
What settings do you need?
You select the lowest amperage that will properly melt the rod and lightly fuse with the casting. Welding cast iron is a superficial job without deep penetration welds. Also, keep in mind that using preheating is like welding with higher amperage.
Of course, you must not set an amperage that is too low. The puddle must be easy to control, fill the edges, and offer a flat bead without slag inclusions. Use the middle value of the packaging’s recommendation and weld on similar scrap metal. After that, adjust the amperage if necessary.
Although direct current electrode negative (DCEN or DC-) inputs less heat in the workpiece than DC+, most cast-iron rods use DC+ polarity.
If you use DC-, you will get an unstable arc and spatter, except if the rod supports DC-.
However, most rods can weld with alternating current (AC) if you encounter the arc blow defect (magnetic interference).
The table below contains amperage examples for cast iron rods. However, each rod packaging always mentions the specific settings: polarity, amperage, and even how much preheating you need.
The amperage is for the flat position with DC current. For vertical, decrease 10-20A and for overhead 5-15 A. With AC, increase 5 or even 10A.
Size | ENi-CI | ENiFe-CI | Est |
---|---|---|---|
3/32″ (2.4 mm) | 40-70 | 45-80 | 50-90 |
1/8″ (3.2 mm) | 70-100 | 70-110 | 80-120 |
If your stick welder has hot-start and arc-force capabilities, it would be best not to use them to avoid additional heat into the metal.
But if your welder supports pulsed current, use it to reduce the total amount of heat in the casting.
3. Clean the surface
Hard-to-weld metals always need a clean surface, and cast iron always has impurity problems. Oil and other contaminants may cover the surface. Because it’s porous, oil can penetrate the surface.
If the casting has absorbed oils, cleaning with acetone, and similar products will not be effective. Use a mild brake cleaner that does not contain chlorine. The welding heat and ultraviolet rays convert chlorine into very dangerous gases.
Read the product’s description to verify that it is not chlorinated and the how-to-use instructions.
The trade-offs of nonchlorinated products are that they are more expensive and very flammable.
You can also remove residual oil by preheating the casting to 750 °F (400 °C) for 15-30 minutes, but it’s costly.
If your casting is free from oil, you remove the casting skin, rust, paint, etc. You can use various ways, such as sandblasting or grinding. If you use an angle grinder, don’t focus on one spot to avoid building up heat.
The area around the joint should be ground to bright metal 1″ on both sides of the joint to prevent impurities from going into the weld metal. The arc will also start easier and run smoother.
After grinding, use a file to remove residual carbon on the joint to avoid turning the weld metal hard and brittle.
A technique to test the casting for trapped contaminants before welding is to pass a small 1/2 – 1″ (12.7 – 25.4 mm) low-amperage bead on the surface close to the repair area.
Then grind the bead to the same level as the casting. Now you check the bead for porosity. If there is porosity, the casting is still contaminated, and you will have problems throughout the entire weld. Before you continue, you must thoroughly clean the joint.
4. Prepare the casting
The best way to remove a crack and prepare a cast iron joint is with a chisel and a hammer. This way, you keep the casting cold, avoid contaminating the porous casting with abrasives, do precise work, and it’s safer than grinders.
After that, you can use a die grinder with carbide burrs or a small-diameter angle grinder, depending on the size and shape of the work.
If you use an angle grinder, move it evenly all over the area and avoid focusing on one spot. Grinding generates high amounts of heat that can affect the casting. When you finish, use a file to remove residual carbon and abrasive material on the joint.
Ensure that the groove is as symmetrical as possible, and always try to weld in the flat position.
Removing cracks
Cracks are the most common damage to repair. If you weld on a crack, it will become longer from the expansion and contraction forces.
To prevent this, drill two holes at least 1/8″ (3.2 mm) wide and 3/16″ (4.8 mm) beyond the ends of the crack. Then, remove the crack by creating a V groove at a safe depth, up to 1/8″ (3.2 mm) from the bottom of the crack. If possible, try not to leave an open root.
The deeper the joint is, the more weld metal you will need to cover it. That will put more heat into the casting.
Broken parts
Because gray iron is rigid and brittle, broken parts fit perfectly with each other. Depending on the size and shape of the broken piece, you can:
- Fit and tack weld the broken part. After that, you can create a V groove, just like when you fix a crack.
- Or you can create small 35-degree bevels on both parts so that a small amount of weld metal can fill them for strength. Then tack weld the broken piece to the casting.
Since typical gray iron has low tensile strength and nickel rods are much stronger, there is no need for full penetration welds if the casting doesn’t have demanding service conditions.
Butt joints
Now, let’s see the scenario where you have a typical butt joint, and your project needs full root penetration.
Since nickel rods don’t offer deep penetration, you leave a wider root gap than similar steel joints.
If you weld a square butt joint from one side and your workpiece is up to 1/8″ (3.2 mm) thick, you can leave a root gap half the casting thickness or even a little wider.

If you can weld both sides, you can go up to 1/4″ (6.4 mm) and leave a root gap half the casting thickness or a bit more, providing that you have a rod big enough to weld this gap.
If the casting is thicker than 1/8″ but cannot weld both sides or your rod is not big enough to weld a wide gap, create bevels on each side and form a single-V groove.
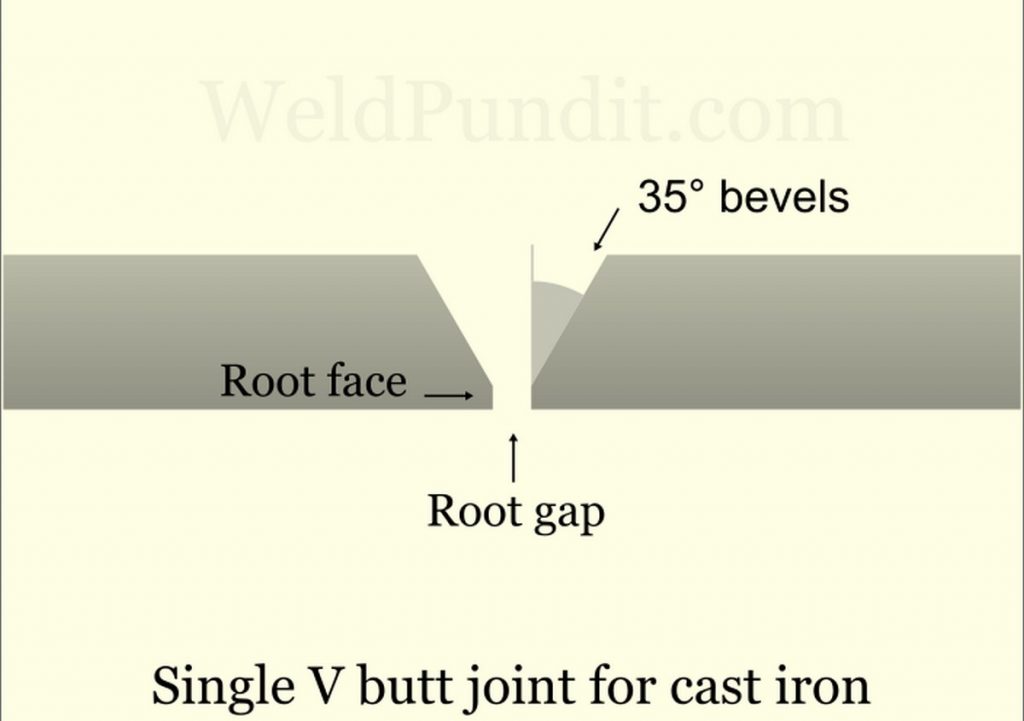
Because nickel weld metal is sluggish and doesn’t flow well, you create wider bevels than similar steel joints, at least 35 degrees on each side. This way, you have improved puddle control.
Furthermore, you don’t leave a thick root face because nickel rods cannot penetrate deep. Therefore, the root face should be no more than half the root gap.
If the casting is between 1/4″ and 1/2″ (12.7 mm), you always create a single-V groove. The root gap for this groove type is up to 1/8″ or a bit more if you have a big enough rod to weld it. Again, the maximum root face is half the root gap.
For thickness greater than 1/2″, it’s recommended to use joints that require less weld metal to spread the shrinkage stress more evenly. This way, you save money since nickel rods are very expensive, and you lower the cracking risk.
A double-V groove is excellent if you can weld both sides.
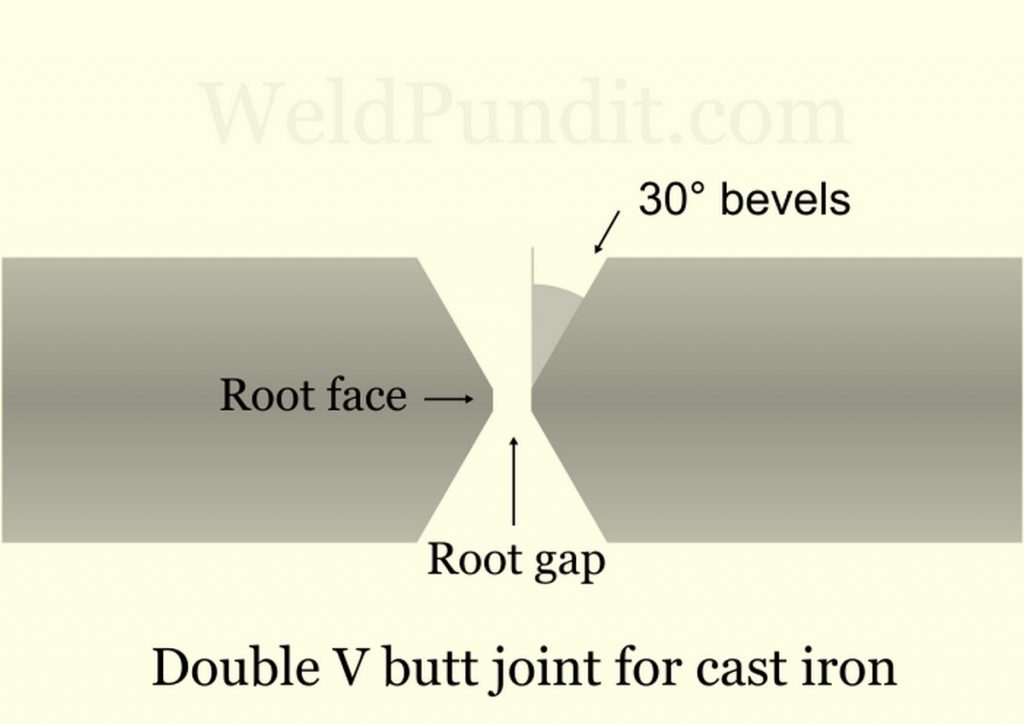
However, if you weld on one side, you want a single-U groove.
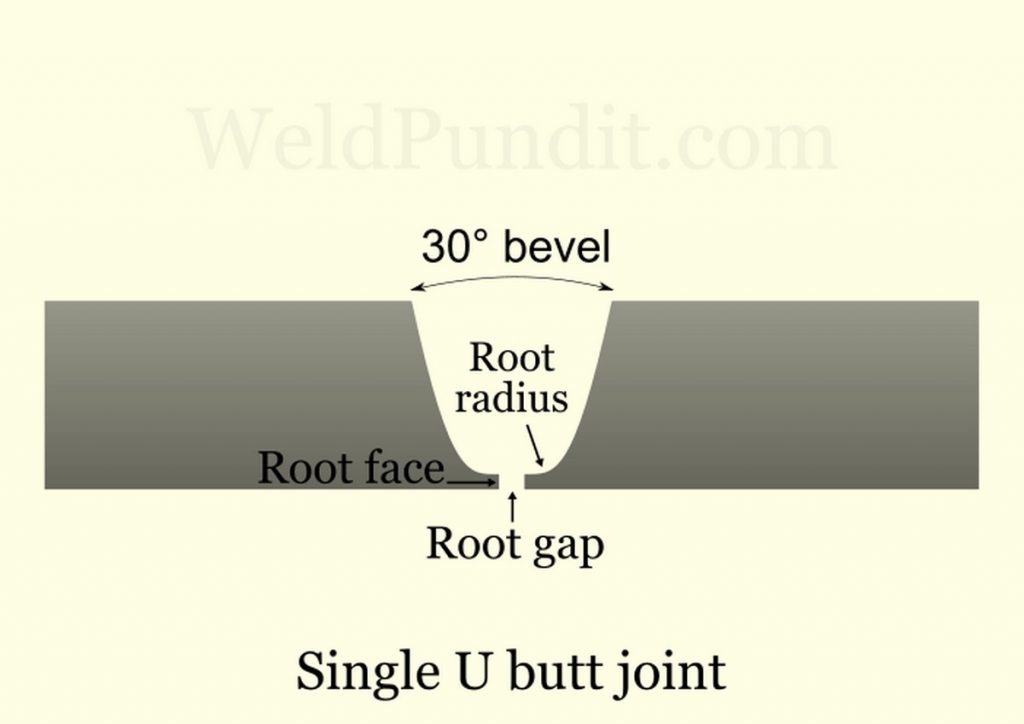
Double-U grooves are recommended for cast iron thicker than 3/4″ (19 mm).
U grooves are always more suitable for cast iron since they require less weld metal, have fewer sharp edges that concentrate stress, and are more symmetrical than V grooves. But you need slow and expensive machining methods to create them.
For the most common cast iron jobs, V grooves are good enough and easy to make.
5. Preheat the casting to avoid temperature differences
Preheating prevents fast expansion when you weld and quick cool-down after welding. With preheating, you decrease the risk of cracking.
The recommended preheating temperature for a medium-sized gray-iron casting is 500 °F (260 °C) using nickel rods. For small castings, you can use half of that.
If you preheat with a flame torch, move it all over the casting and concentrate on the thicker parts. This way, you preheat it evenly. Next, use the temperature stick (or the digital thermometer) on the surface occasionally to check the temperature. If the stick melts evenly all over the casting, you are ready to weld.
When you preheat the casting, you must weld it in a reasonable amount of time to prevent it from getting colder. If you use the temperature stick and it doesn’t melt, reheat the casting.
You must avoid any cold drafts during welding. If the casting is big, insulate it with welding blankets or similar equipment.
If the casting cracks at any point, chances are you didn’t avoid the temperature differences in the metal with enough preheating.
6. Weld short beads to prevent uneven temperatures
When you weld brittle metal, you weld very short beads to avoid putting too much heat inside them. The general rule is to weld 1″ (25.4 mm) beads. The length depends on the casting thickness:
- For a 1/4″ thick casting, you can weld a 1″ bead.
- For a 1/4 to 1/2″ casting, weld a 2″ bead.
- And for 1/2″ and thicker, weld a 3″ or slightly longer bead.
The heat that goes into the metal depends on the way you place the beads. To reduce the cracking risk, you don’t place each bead right next to the other. Instead, you spread them along the joint to spread out the heat.
Below is an image with an example of how to spread the beads on the joint.
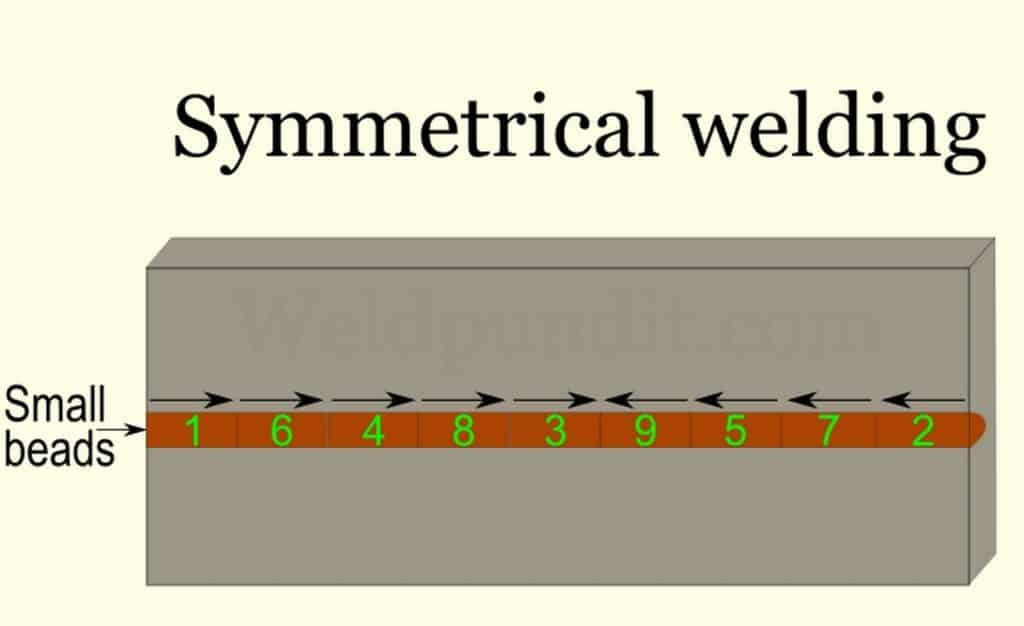
Some additional tips:
- All cast-iron rods have a flux covering that is sensitive to moisture. Keep them dry to avoid an unstable arc, rod sticking, excess hydrogen in the metal, and other defects.
- The traveling speed greatly affects the heat input. For this, you should travel as fast as possible without creating any defects from it.
- Straight beads (or stringers) without weaving the rod are more suitable.
- Always keep a short arc length, no more than the rod’s wire diameter.
- Each time you weld, you should avoid striking the arc on the casting, but in the joint or on the previous beads.
- Always fill the crater. If there is a gap, the shrinkage forces can crack it.
- If a crack appears when welding, stop and drill holes at both ends to stop it from expanding.
- If your casting is irregular, weld the thicker areas first.
- Connect the working (or grounding) clamp to a clean area on the casting, not on the table.
Avoiding turning red-hot the area you weld is a reliable indication that you do not overweld the casting.
7. Peen each bead to prevent shrinkage stress
Peening is when you tap all over the red-hot bead with a small rounded hammer immediately after you finish it. Start from the crater and use rapid blows that will lightly indent the weld metal.
Peening will stretch the weld metal and counter shrinkage forces. This will prevent residual stress in the bead and will reduce the cracking risk.
However, hitting the bead too hard or too long will harden it, making things worse. We call this work hardening.
You may also use a rounded chisel or an electric needle scaler with round needles.
While you are peening, you also remove the slag covering. Then, use your wire brush to clean the rest of the slag before you pass another bead.
8. Reheat the casting to fix temperature differences
After welding, you must ensure the casting has at least the same preheating temperature, spread out evenly. You check the temperature and reheat the casting if necessary.
9. Protect the casting so it can cool down slowly
The final step is crucial to preserve the metal’s characteristics and prevent cracking. The slower you cool down the casting, the better.
You must insulate the entire casting to cool down evenly until it reaches room temperature, and you can touch it.
If you preheated the casting with an oven, use it again to cool it down. Otherwise, you can cover it with welding blankets, similar fiberglass material, or dry sand.
In the second part of the article, let’s see how to weld cast iron without preheating.
Stick weld cast iron without preheating
There are many situations when you might consider welding cast iron without preheating:
- Sometimes castings are too big or complicated to preheat correctly.
- The damage is short cracks or superficial wear.
- You might not have the necessary preheating equipment.
- You cannot dismantle the part, and it will crack if you preheat it.
- The casting is small and simple, and you want to avoid the trouble and the costs.
It is possible to stick weld cast iron without preheating using nickel rods (ENi99 and ENi55), short beads, and peening. However, lack of preheating will always make the casting weaker next to the weld and more prone to cracking in the future. Welding without preheating is also called cold welding.
Without preheating, you also skip the post-heat and cool-down steps. The main concern is to minimize the heat input and the width of the heat-affected zone (HAZ) to the absolute minimum. The HAZ is the area next to the bead. To do this:
- Use only cast iron nickel rods because they do not penetrate deep and have high ductility.
- Use the lowest amperage to melt the rod properly and achieve low fusion between the weld metal and the casting.
- Weld short 1/2″ (12.7 mm) to 1″ (25.4 mm) straight beads.
- Always peen the bead when it’s red hot.
- After each bead, you stop and let the bead cool down until you can touch it comfortably with your bare hands. That’s around 100 °F (38 °C). This step is the most important one when skipping the preheating step.
- After that, you weld another short bead and repeat until you finish.
However, skipping the preheating step doesn’t mean you can weld cold cast iron. Welding in a cold environment will always give poor results. To prevent this, warm the casting to room temperature, 75 °F (24 °C), before starting.
Keep in mind that lack of preheating is risky, and you should consider preheating when::
- The casting is very thick.
- Has demanding service conditions.
- Is damaged in the center. Cracks or broken parts at the edges can be welded easier with less or no preheat.
If your stick welder has hot-start and arc-force capabilities, it would be best not to use them to avoid additional heat into the metal.
More Weldpundit articles